Nancy Shadrix and Chase MacKarvich of Tie Down Engineering with one
of Tie Down's three Laser Tube Cutting Centers. The switch to SCS has
lowered scrap rate at these and Tie Down's table lasers that cut sheet. |
fabricating division – Industrial Laser
Solutions (ILS). ILS operates three
advanced 3D laser tube cutting
centers and any rust on the tubes |
|
really hampers efficiency. ILS had |
been outsourcing a process called 'Eco Cleaning' to remove the rust prior to lasering, but it was expensive and added cycle time. The switch to SCS eliminated that problem and kept the tube lasers humming along.
Seeing the advantages gained in tubing, Shadrix wanted to investigate using SCS for other TDE parts. That was a tall order because TDE’s operations are so extensive. Occupying four Atlanta manufacturing sites totaling over 400,000 sq.ft., Tie Down Engineering seems like a contract manufacturer on steroids. It does stamping, bending, welding (including robotic) turret punching, flat bed and tube laser cutting, CNC boring, milling and grinding . . . even plastic injection molding! That versatility comes in handy when you manufacture over 6600 SKUs.
Of course, it wasn’t always that way. TDE started out in the garage of founder and President Charles “Chuck” MacKarvich in 1971. He was designing and building better “tie downs” – anchoring systems that secure mobile homes in place against high winds. As his tie down systems gained popularity, MacKarvich’s entrepreneurial drive took TDE into products as diverse as boat trailers, mailbox posts and roofing contractor safety products. |
"Our sales doubled roughly every five years and today we have divisions that serve Marine, Roofing/Construction, Manufactured Housing, Cable Products and Trailer Component manufacturing for OEMs.” explains MacKarvich. “Our Engineering staff has a reputation for design innovation, and our Operations teams are obsessed with efficient manufacturing and superior quality. We’ve also developed a capital investment philosophy for the ILS Division we call ‘High Operating Leverage.’ It's selecting reliable manufacturing equipment with the automation and options to let us condense cycle time and improve quality on all the parts we think could use that process."
|
MacKarvich’s son, Chase MacKarvich, is a leader of ILS responsible for matching that growing parts list to ILS’ state-of-the-art machine tools in a way that boosts overall productivity. Chase oversaw the introduction and evaluation of SCS sheets in the various ILS processes that consume flat rolled low carbon steel.
“We saw a lot of advantages to SCS,” Chase recalls. “Our welding cells gained efficiency and weld quality improved due to the cleanliness of the SCS material. Our flat bed lasers run faster with SCS, and we are more confident our ‘lights out’ laser operations will run without a hiccup. Most importantly, SCS gives a cleaner cut, even at the tightest tolerances, and that lowers scrap levels from lasering. And the paint finish on SCS parts looks better cosmetically, so now we need to see if we can lean out paint prep on SCS parts as we’ve been told we should.”
Since SCS sheets got the ‘OK’ from production testing, Shadrix has switched over nearly all the company’s flat rolled buys to SCS. She sources hot rolled from 12 gauge up to 0.250”, with regional SCS Producer Feralloy doing the SCS processing of this material at its Charleston, South Carolina facility.
|
|
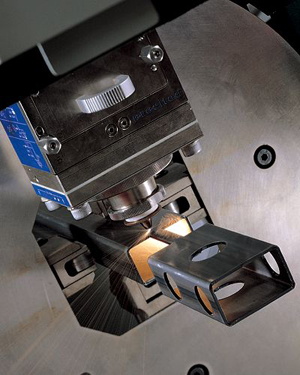 |
|
“I can’t emphasize enough how the cleanliness and rust resistance has helped us,” says Shadrix. “SCS has a much longer ‘shelf life’ so SCS parts that go to plating or painting don’t get rejected for rust and sent out for that expensive Eco Cleaning anymore. It also helps me manage inventory. I’ve consolidated what were separate hot rolled black and HRPO orders into SCS. And if I find a really good buy on hot rolled I can jump on it, knowing I can have it SCS’d and it will keep in my inventory without rusting.”
Does Shadrix pay a higher price for the SCS sheets? “SCS costs more than hot rolled black, sure, but we more than offset that with the processing savings. SCS is actually cheaper than HRPO because we eliminate the pickling charge and freight to and from the pickler. So we’re saving money with SCS and making a better product. That falls right in line with our ‘High Operating Leverage’ philosophy.
And it all started with a simple tube sample that just didn’t rust!”
|
|
SCS Fabrication Guidelines A Good Read
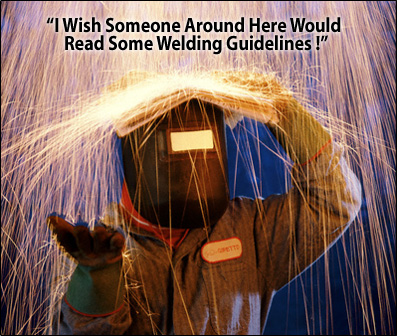 |
The conventional thinking is that nobody reads anymore. We surf, we sample, we podcast, but who has time to read?
If you're using or trialing SCS and haven't read the SCS Fabrication Guidelines, you would do well to make the time. (Hey, we're not talking a lot of time here - it's only 10 pages).
The SCS Fabrication Guidelines describe and explain a number of best practices that help you get the most from welding, laser cutting, paint prep and other processes applied to SCS.
Following the guidelines has helped many SCS users capture advantages like gains in laser cutting speed or reduction in weld wire feed rates.
|
|
|
But is SCS really so different that it |
needs it's own 'how to' guidelines? In some cases the answer is " YES" simply because SCS is so clean. For example, leaning out your paint prep regimen when using SCS is a direct result of that cleanliness . . . and the Guidelines take much of the guesswork out of deciding what 'leaner' paint prep regimen could work best for you.
In other cases, the answer is "NO" because the guidelines would improve your performance (or lower your cost) whether they're applied to SCS, HRPO or hot rolled black. For example, many SCS users find the recommended welding gas specs contained in the Fabrication Guidelines improve weld quality for all their hot rolled material, not just SCS. (However, the improvement for SCS is often greater – again, because of its cleaner surface.)
That's not a lucky coincidence; it's a result of how the Guidelines were developed . Each SCS Fabrication Guideline spec was developed in conjunction with recognized experts in that particular technology area. These experts started with the fundamental recipes and best practices they know work well in most circumstances and then, through carefully controlled trials, further refined and optimized them for SCS. But the fundamental recipes often improve performance for HRPO or hot rolled black as well, so why not use them for these materials?
Well, you can't use them if you don't know about them, and all too often the operator on the shop floor doesn't know the SCS Fabrication Guidelines even exist. That can lead to a disappointing initial experience with SCS because the process settings the operator normally uses may not be optimized for any hot rolled steel .
How to solve this problem?
Step 1: Good communication from the SCS supplier to the SCS customer so the customer is informed and
prepared when they begin using SCS.
Step 2: A little light reading . . .The SCS Fabrication Guidelines . . . which will never make anyone's Bestseller
List, but just might help you lower your fabrication and paint prep costs considerably.
You can download the SCS Fabrication Guidelines by clicking on this link.
|
|
 |
|
|