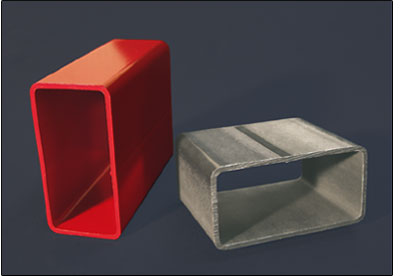 |
This company's biggest problem was rust claims - not unusual given they were producing their tubing from hot-rolled black material. They learned of SCS, obtained samples, and set the samples outside "in the elements" for several weeks. When they saw no rust on the samples, they were ecstatic.
"I had to actually convince them SCS would eventually rust, even though their samples fared so well setting outdoors," explained TMW President Kevin Voges. With this understanding, the tube producer sent a coil of 11 gauge hot-rolled black to TMW for
SCS treatment.
During processing of the coil at TMW
|
 |
These sections are cut from 4 inch structural tubing produced from SCS coils.
The very smooth, clean surface makes them both 'ready-to-weld' and 'ready-
to-paint' as they come off the tube mill. |
the tube producer representative was
pleased to see benefits of SCS
"coil conditioning" where light-to-
medium coil breaks and surface rust |
|
were both completely removed! |
The tube producer representative also saw how the SCS Coil Line removed edge wave in the coil. He pointed out that shape problems like edge wave can result in tube production problems, so their elimination is a big benefit. When the SCS coil arrived back at the tube producer's plant, they slit the coil and began running it on their tube mill. "Not only was the SCS very clean, but also very flat going into the mill," observed the plant manager.
Coming out of the mill, the quality of the SCS tubes was impressive -- excellent shape, a very smooth surface and no microcracking on the outside of the four corner bends. To test the rust-inhibitive qualities of the SCS tubes, samples were again exposed to the elements for a month. Again, no rust developed. The plant manager concluded, "These SCS tubes are ready to weld into structures, right off the mill. What's more, they will dramatically reduce rust claims which are our biggest quality headache."
|
He sees tube mill changes that should be made to
fully leverage SCS. One is to move from using an oil-based to water-based coolant in the tube mill. This
will remove any oil from the SCS tubing that keeps it
from being 'ready-to-paint' right off the mill. Also, the coolant will have to be filtered better so traces of scale and mill dirt aren't deposited on the otherwise very
clean SCS surface.
While the SCS performance as a tubing material has been impressive, another phase of SCS tubing trials
will be conducted after the coolant system changes
are complete. "Line speed is often limited by the seam
welding process," stated the tube producer's plant manager. "We're hopeful the cleanliness of the SCS surface will improve 'weldability', giving us an overall production speed increase."
|
He concluded," SCS has already shown its ability to reduce our big quality concern - rust - and allow us to deliver a better product that is 'immediately usable'.
Any increase in production speed we experience with
SCS would just be 'icing on the cake."
|
|
 |