 |
 |
 |
 |
 |
 |
 |
 |
 |
 |
 |
|
|
|
|
|
|
|
|
|
|
Recent salt spray corrosion testing of SCS panels produced an important result -- you can achieve extended corrosion resistance using just a single stage water rinse paint prep. That's BIG potential savings to manufacturers who paint their parts.
Salt spray fog chambers are used to test corrosion resistance of pre-treatment and paint formulas. Treated, painted samples are scribed through to the bare metal, then exposed to a 5% salt fog atmosphere, simulating accelerated exposure to the elements. Rust forms in the scribed stripe, causing paint to 'creep' away from the scribe. The rate of creep indicates the paint system's ability to retard further rusting of unexposed steel.
|
|
|
With no pre-treatment, even clean hot rolled with high quality powder coat paint will show significant creep by 200 hours exposure (see graphic at right). And you'd never think of painting P&O without a pre-treatment (paint doesn't adhere very well to an oil film). So to improve a paint's effectiveness, steel parts undergo pre-treatment consisting of both chemical and rinse stages. The most common chemical stage is an iron phosphate and water solution. The iron phosphate improves a paint's adhesion and uniformity, which inhibits the spread of corrosion beyond damaged areas.
However, the recent SCS tests exposed four SCS panels that received no phosphate at all - only a water rinse prior to a single powder coat with a common, good quality polyester paint. At each inspection interval up through 288 hours, the SCS panels showed no noticeable paint creep. The next inspection interval at 384 hours finally showed significant creep, but the SCS panels had already demonstrated 300 hours corrosion resistance using just a water rinse pre-treatment (see test results here). You simply cannot get performance like that from P&O or hot rolled.
A leading paint system consultant who reviewed the SCS results agrees. He states that the SCS performance is 'truly impressive' and suggests leaning down an existing phosphate pre-treatment to a two-stage rinse: "The first stage should use a |
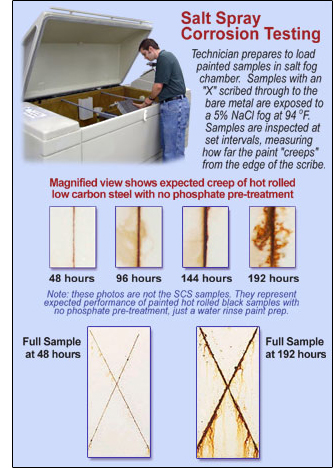 |
low-foaming surfacant at 0.1% concentration (by volume) in water as a recirculating stage. Use a |
|
|
|
clean, overflowing water rinse as the second stage. For very clean SCS (light handling dirt), it may be feasible to use only the first stage and reduce the surfacant concentration to 0.01% - enough to give the SCS low surface tension so paint 'wets out' evenly while curing."
|
The Manufacturers who send parts out for painting because they lack pre-treatment systems may now consider painting SCS parts in-house. Those with pre-treatment systems may 'lean out' their paint prep as noted above. Stan Vallis, operations manager of Custom Cabinets & Racks (see Issue #10) has already begun. After switching from P&O to SCS nearly a year ago, Vallis found he needed to change out his iron phosphate solution much less often because SCS is so clean. He also lowered his iron phosphate concentration from the 3% he used with P&O to just 1% with SCS, and his paint performance has never been better. With SCS, Vallis is proving in practice what the laboratory proved in principle: SCS can help you save big on paint prep without compromising on paint performance.
|
|
 |
 |
 |
 |
|
|
|
|
|
|
|
 |